Process Quality Leader - #1670757
Unilever Brazil
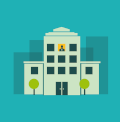
Job Title: Process Quality Leader
Location: Leeds Factory
JOB PURPOSE
As the largest producer of deodorants in Unilever’s global network, the Leeds SU plays a crucial role in supporting Unilever’s ambitious growth targets. Our focus is on delivering perfect products to both European and cross-regional markets, with product quality being a key enabler of this growth.
The Process Quality Leader will support the leadership team in driving quality performance and awareness at the operational level. Reporting to the Site Quality Manager, the Process Quality Leader will manage semi-finished products and chemical raw materials, oversee quality technicians and laboratories, and provide flexible support to operations. Additionally, the Process Quality Leader will assist the Site Quality Manager in developing strategic improvement plans and programs.
RESPONSIBILITIES
The primary focus will be the reduction of quality losses by following key areas of responsibility:
Process Innovation and Implementation
- Implement and manage new/modified formulations, processes, and chemicals, including risk management, test methodology, specifications, and washout protocols.
- Manage inspection schedules to ensure material compliance within specifications.
- Approve PFDs and manage the PFD database for product batches.
Management of Raw materials and Semi-finished Product
- Manage testing methods and equipment for incoming chemicals and SFP to ensure timely release.
- Ensure robust processes for managing materials and traceability to limit consumer safety hazards.
- Support supplier onboarding and review processes, including visits to new suppliers/sites.
- Optimise raw material and SFP specifications through statistical review to drive improvement. This will include minimisation of product giveaway, demonstration of specification compliance and reduction or elimination of Quality testing where justified.
- Create Quality Certificates required for product export.
Process and Tank Farm
- Maintenance of three plant side testing and main laboratories.
- Analysis and equipment for the Wastewater treatment plant, Water Plant system and Deodorant Blending Skids.
- Go-to-person for analytical support and key contact for factory processing.
- Sets all Good Lab Practices of the main and plant side labs, including Managing calibration, maintenance and verification schedules for laboratory equipment.
- Develop and sustain competencies within the Process Quality team Process and Tank Farm operators.
- Carry out Training in support of the wider Quality Programme (including any training related to process stock and verification of operators).
Quality Incident management
- Responsible for the management of operational quality incidents using internal processes (quarantine, audit testing and decision on fate of stock) of non-conforming material/ process related incidents/ supplier incidents.
- Work with procurement to ensure local quality requirements for new and existing suppliers are communicated and ongoing Supplier issues are effectively managed.
- Make quick, effective decisions on substandard stock to minimize quality non-conformance impacts on the consumer, market, logistics and factory operation.
- Act as primary contact for major quality incidents both internal and external.
- Lead and support potential recall activities, deputizing for the Site Quality Manager when needed.
- Drive problem solving activities for quality incidents and support other incidents by providing technical knowledge and expertise.
- Identifies key Quality losses using continuous improvement tools with aim to reduce/eliminate these.
- Identify and investigate consumer complaint trends to drive improvements by determining RCA and CAPA implementation.
Legislative
- Ensure that legislative requirements are met in process areas and on packing and process lines in respect of the 7th Amendment to the Cosmetics Directive (washout procedures). In particular, ensure wash-out matrices are developed, maintained and effectively communicated to all packing lines and process areas. Verification of these requirements also required.
- Management of Site Weight Control. Ensure processes are in place that demonstrate compliance to weights and measures legislation and minimise product giveaway therefore minimising costs to the business.
- Understand the different technologies that help manage weight control such as Heuft level detectors and Garvens checkweighers. Ensure operators, craft, and quality team members have an appreciation of weight control and understand consequences of failure. Develop and implement systems that make the recording of manual weight checks as robust and user friendly as possible.
- Ensure check systems (challenge cans) are in place and maintained that can demonstrate reject mechanisms for under/over weights are functioning correctly.
Product Safety & Quality
- Ownership of Quality related documents and processes which are part of the site Integrated Management System (IMS).
- Key member of product safety and HACCP team - responsible for compliance with relevant Unilever UQPs/GMPs.
- Understand and drive compliance to the site product safety and quality policy and standards held.
- Pivotal role in internal and external Product Safety and Quality audits- including BRC and ISO standards.
- Perform regular quality audits and inspections, and use the findings to drive the performance improvement. These may include Departmental Inspections, Internal and External Audits and Quality Pillar Self Assessment Reviews.
Job functionalities
- Direct Line Management Responsibility, absence management, development of team via PDP process, etc.
- Key user for SAP QM inspection module and schedules.
- Manipulate analytical data for SPC and review purposes.
- Be involved / lead audit and investigation processes (both internal and external).
- Key contact for processing (EU R&D). Participate fully in EU R&D meetings to ensure current and long-term improvements are developed and worked upon.
- Champion quality awareness activities which promote the development of a quality culture ie. Quality Theme of the Month and World Quality Week.
- Monitor and measure key Quality performance, including monthly KPI reporting and input to Environmental measures (pH, COD of effluent).
Sourcing Unit Operations
- Provide analytical support for managing environmental KPIs and production waste streams.
- Understand and enforce process safety systems and site safety policies.
- Understand the importance of behavioral safety and carry out Safe Acts Visits.
- Understand and enforce site safety policies & rules.
- Conduct risk assessments and contribute to business risk acceptance.
- Responsible for use of principles of workplace organisation (5S) in own areas.
ALL ABOUT YOU
Experience and skills
- Degree level in Chemistry preferred or in other science discipline required.
- Working SAP knowledge, preferably with stock management and quality inspections.
- Management of stakeholders (suppliers, operations, R&D).
- Laboratory experience and strong analytical skills.
- Advanced problem-solving skills and statistical analysis.
Personal Qualities
- Self-motivated, positive attitude.
- Good team worker.
- Proven record of continuous improvement.
- Able to engage, empower and enable people.
- Comfortable in challenging situations.
#J-18808-Ljbffr
How to apply
To apply for this job you need to authorize on our website. If you don't have an account yet, please register.
Post a resumeSimilar jobs
Health & Safety Coordinator (internal)
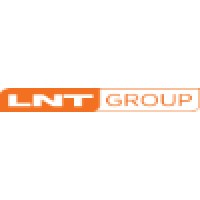